www.tillverkning-sverige.com
11
'19
Written on Modified on
Hur Sandvik byggde världens första 3D-printade, okrossbara gitarr
Rockstjärnor har slagit sönder gitarrer i årtionden, och Sveriges egen virtuos Yngwie Malmsteen är inget undantag.
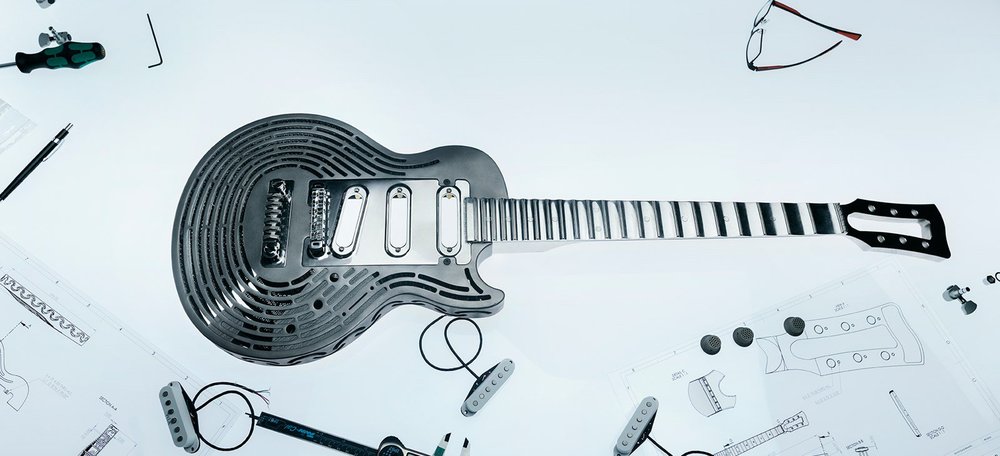
I det här projektet samlade Sandvik experter från hela företaget för att demonstrera hur de kunde använda hållbara, moderna tekniker för att tillverka något som både har mycket hög noggrannhet och som samtidigt är otroligt tåligt.
– Vi tillverkar inte konsumentprodukter längre, så många känner inte till hur avancerade våra metoder är, säger Klas Forsström, chef för Sandvik Machining Solutions. Genom att tillverka en okrossbar gitarr åt en kräsen musiker som Malmsteen visar vi upp vår kompetens som vi utnyttjar vid alla komplicerade tillverkningsutmaningar.
Sandviks tekniker samarbetade med den kända gitarrdesignern Andy Holt från Drewman Guitars för att kunna matcha Malmsteens krävande musikaliska standard och blixtsnabba spelstil.
Världens första okrossbara gitarr
Henrik Loikkanen, teknisk processutvecklare på Sandvik Coromant, har spelat gitarr sedan ungdomen och har haft Malmsteen som idol. För att förstå vad som händer när Malmsteen förstör ett instrument studerade Loikkanen videoklipp på YouTube.
– Vi var tvungna att designa en gitarr som både låter bra och som inte går att slå sönder på de sätt som man kan slå sönder en gitarr, säger Loikkanen. Den konstruktionsmässigt största utmaningen var den kritiska fogen mellan halsen och kroppen, som är det ställe som oftast bryts av på en gitarr.
Sandviks tekniker eliminerade helt enkelt fogen mellan hals och kropp. I stället frästes gitarrens hals och greppbräda ut i en maskin ur solida stänger av återvunnet rostfritt stål, en konstruktion som aldrig tidigare hade provats. Både halsen och greppbrädan sträckte sig in till ett rektangulärt centralstycke som fästes inne i gitarrkroppen.
Avancerade skärdata
Långa, slanka komponenter som greppbrädan och halsen är särskilt känsliga för skevhet. Med hjälp av avancerad programvara kunde Sandvik Coromant simulera fräsningen digitalt före det första ingreppet, så att man kunde välja rätt verktyg, spara tillverkningstid och säkerställa effektiva processer.
– Precisionen var kritisk, säger Henrik Loikkanen. Vår programvara bygger på åratals erfarenhet och lämnar rekommendationer om verktyg och skärdata som hjälpte oss att fräsa greppbrädan ner till den utmanande tjockleken på bara en millimeter på en del ställen.
En 3D-printad titankropp i flera lager
Under tiden hanterade man en annan utmaning: hur man skulle tillverka gitarrkroppen – en extremt komplicerad design på grund av behovet av både hög styrka och låg vikt.
Sandvik, med sin världsledande expertis inom metallpulver och additiv tillverkning, bestämde sig för att 3D-printa kroppen. Genom att använda laserteknologi smältes fina lager av titanpulver samman, vart och ett tunnare än ett hårstrå, och byggde successivt upp en tredimensionell gitarrkropp i titan – direkt från en digital design.
– Med hjälp av additiv tillverkning kan vi skapa lättare, starkare och mer flexibla komponenter med invändiga strukturer som skulle vara omöjliga att tillverka med traditionell metallbearbetning, säger Amelie Norrby, en ingenjör inom additiv tillverkning som deltog i gitarrprojektet. Och 3D-printning är dessutom mer hållbart, eftersom vi bara använder exakt det material som behövs för komponenten, vilket minimerar spill.
Materialvärlden
Tomas Forsman, specialist inom forskning och utveckling på Sandvik, insåg att gitarren behövde en särskild struktur som var stark, styv och lätt. Han föreslog en ILS-konstruktion (Isotropic Lightweight Structure), den starkaste strukturen som finns för en viss vikt.
– Det ser ut som vilket ramverk som helst, förklarar Forsman, men det är faktiskt styvare och lättare än något vi har sett tidigare.
Forsman visste också exakt vilket material som ILS-strukturen skulle tillverkas av: hyperduplext stål, en sort som endast Sandvik producerar. Han ville lägga det hyperduplexa ILS-materialet mellan gitarrens hals och greppbräda.
Sådana här samarbeten är nyckeln till framtiden.
Men greppbrädan fick inte utsättas för någon vridning – ett problem vid sammansvetsning av långa, tunna komponenter. Genom analyser och tester finjusterades svetsprocessen, tills ILS-lagret kunde integreras problemfritt.
Forsman menar att gitarrprojektet och det samarbete som krävdes illustrerar hur Sandviks djupa kompetens och erfarenhet kan lösa unika utmaningar, också inom snäva tidsramar.
– Sådana här samarbeten är nyckeln till framtiden, säger Forsman. Våra kunders utmaningar fortsätter att växa och bli alltmer komplexa. Vi måste få vår kompetens att samverka med våra partners och kunder, och fortsätta att utveckla nya sätt att hantera dessa utmaningar.
Live på konserten
När gitarren var klar gav Sandvik den till Yngwie Malmsteen för det ultimata testet. På en klubb i Florida drog Malmsteen igenom flera låtar, och gjorde sedan sitt bästa för att slå sönder gitarren genom att svänga den mot högtalare, scenelement och golvet.
– Den här gitarren är ett monster, utbrast Malmsteen efter att ha gett upp sina demoleringsförsök. Sandvik vet helt klart vad de sysslar med. De har gjort arbetet, lagt ner de timmar som behövs. Det kan jag relatera till. Resultatet är helt otroligt. Jag gav allt, men den gick inte att ha sönder.
www.sandvik.com