www.tillverkning-sverige.com
24
'11
Written on Modified on
Omfattande kompetens inom stål och plast
KABELSCHLEPPs kablar och slangbärarsystem tar i ett världsunikt projekt varje detalj i beaktande
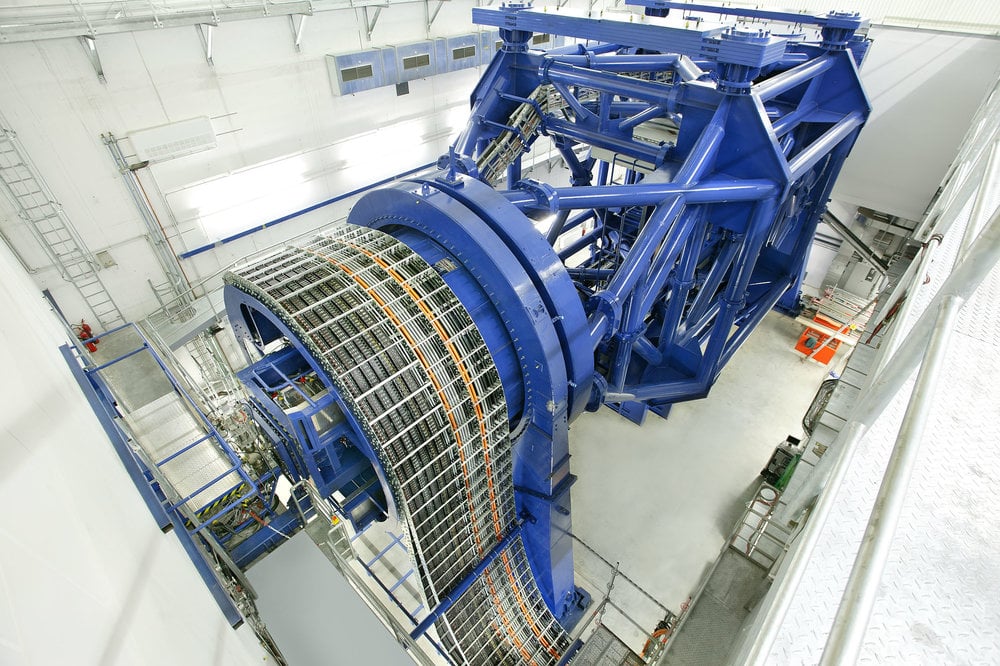
Tillverkare av verktygsmaskiner och system kräver ett stort antal komponenter för formgivning. För särskilt krävande eller komplicerade applikationer måste leverantörer erbjuda, inte enbart lämpliga produkter, utan även kunskap och utvecklingskompetens. En orsak till varför MT Mechatronics inte fann något alternativ än att arbeta med Kableschlepp i detta verkligen suveräna projekt.
Modern teknologi har förändrat nästa alla aspekter av livet till mer bekväma – i många fall är det mycket viktigt. Detta gäller särskilt inom området för medicinsk teknik. Ambitiös forskning och utveckling pågår inom många områden i förhoppning om att finna innovativa lösningar till problem. Detta har nu resulterat i ett system för behandling av tumörer hos cancerpatienter: Heidelberg Ion Beam Therapy Center (HIT) vid Heidelberg Universitetssjukhus är ett delvis underjordiskt högteknologiskt center på tre våningar, i storlek ungefär som en fotbollsplan, där tunga joner accelereras till tre fjärdedelar av ljusets hastighet och sedan styrs exakt in i tumören. Tunga joner skiljer sig avsevärt från vanlig röntgen eller gammastrålning, efterson de verkar på djupet. Tack vare state-of-the-art-teknologi kan de riktas med stor precision, vilket ger mindre skador på omgivande frisk vävnad.
HIT har ett antal egenskaper som gör det världsunikt. En av dem är utlastningsanordningen, en vägledande roterande stråle för tunga joner, i motsats till de två horisontella stationerna för strålbehandling, där jonstrålen släpps ut från ett sugrör i väggen och börjar verka på patienten som är placerad framför den. I det tredje behandlingsrummet styrs balken mot patienten från olika håll för att uppnå den optimala behandlingsvinkeln. Med extrem precision avviker balken från målet med högst en halv millimeter.
Bryter ny teknisk mark
Detta är möjligt genom den omfattande utlastningsanordningskonstruktionen bakom kulisserna. Den rörliga balken av överföringssystem med vakuumrör är upphängd i en komplex ram som liknar de som används för radioteleskop. Denna koloss är tre våningar hög med en total vikt på 670 ton, varav 600 är lösa. Utveckling, leverans, montage och drifttagning av utlastningsanordningen vilar på MT Mechatronics GnbH i Marinz, i samarbete med Centre for Heavy Ion Reserach, Darmstadt. MT Mechatronics är en del av MT Aerospace AG i Augsburg, en etablerad leverantör till flyg- och försvarsindustrin och en erfaren systempartner för antenner, teleskop och mekatroniska system.
Första uppdraget för MT Mechatronic var att genomföra en studie för undersökning av de fysiska förutsättningarna att använda en lämplig struktur till att styra jonstrålen, som är paketerad och överförd i magneter som väger ton, samtidigt som hänsyn tas till effekterna av fysiska krafter och temperaturförhållanden. Byggnaden uppfördes enligt de ursprungliga planerna, men under projektets genomförande stod det klart att det fanns ett mycket begränsat utrymme för utlastningsanordningen. Även om detta problem skulle kunna åtgärdas med hjälp av ett fåtal konstruktionsändringar, fanns fortfarande ett stort hinder som måste övervinnas: kabel- och slangtransportörer som hjälper till att få liv i kolossen så att den kan användas för tumörbehandlingar. Redan detta var en utmaning, med tanke på de mycket komplicerade förhållandena, men det hela skulle ju också utformas extremt kompakt.
- Även för mindre krävande applikationer är få kablar och slangar rätt ofta ett stort problem för transportören. Lösningen baseras främst på användarens specifikationer, säger ingenjör Martin Süß från System Engineering på MT Mechatronics.
Gällande portalkranar var den huvudsakliga inriktningen på de typiska kraven att peka på riktigheten i balkens vägledning och justeringens hastighet.
- Vi var hela tiden uppmärksamma på dessa punkter under projektets gång. Och till sist blev slutsatsen: vi kommer att behöva lägga ytterligare en kabel där.
Süß vet detta av erfarenhet. Och eftersom erfarenheten visar att det inte är så enkelt att ordna behövdes en partner på samma nivå. Det är därför MT Mechatronic, specialist på prototyper av byggnadskonstruktioner och pilotprojekt, litar på erfarenhet och know-how av en annan specialist. Som uppfinnare av kabel- och slangbärare, och som företag med ett brett spektrum av produkter, har Kabelschlepp inte enbart rätt komponenter för att tillhandahålla skräddarsydda lösningar, utan framför allt decennier av praktisk erfarenhet med bred variation av applikationer och miljövillkor. Ingenjör Klaus Scheidel från Project Management hos MT Mechatronic, och den som ansvarar för byggandet av utlastningsanordningen, vet även detta:
- För oss är erfarenhet den avgörande faktorn, liksom flexibilitet och kreativa idéer. Leverantörer med dessa egenskaper identifierar sig med problemen och är fast beslutna att hitta en lösning, även när det blir komplicerat. Och Kabelschlepp har klarat detta test med utlastningsanordningen.
Masterförändringar planeras
Andreas Wienbeck, från kabel- och slangtransportsystemets projektplanering i Siegen, gav sitt stöd till utlastningsanordningsprojektet. Från hans mångåriga erfarenhet vet han följande:
- Den ursprungliga situationen är alltid densamma: du tar ett definierat antal kablar och slangar som måste läggas samt vissa villkor för tillämpningen. Dessa används i planerigen. Med finns alltid ett stort antal förändringar och andra saker som måste bearbetas innan allt fungerar rätt.
Det var samma sak med utlastningsanordningen. Till de kablar och slangar som ursprungligen var planerade anslöt sig ett stort antal nya. Till sist skulle en kabel och en slang som väger 150 kg /m, och upp till 15000 Nm, täckas vilket innebar att valet av material för transportörsystemet skedde mer eller mindre automatiskt.
- Det är inget tvivel om att stål är vårt val av material, säger Wienbeck. Stålets bärare är också strålningsresistenta på lång sikt, också det en viktig faktor när det handlar om driften av portalkranar.
På ett tidigt stadium stod det klart att på grund av det kraftigt ökade antalet kablar och slangar skulle det planerade transportörutrymmet inte vara tillräckligt. Dessutom var strålningsvärmen på kablarnas ytterhölje i vissa fall över 70°C, de som ger stöd till 130 metriska ton magnetbalkarna. På grund av den värme som alstras var kompensationen för kabel- och slangdragning inte längre möjlig – det var en fara med att sätta fast dem.
- Strömförsörjningskablar till magneter bär en enormt stark ström. För att skydda systemet mot överhettning kyls kablarna med vatten i kylslangar. Tyvärr visade det sig att värmeutvecklingen ändå var ganska hög, säger experten från Kabelschlepp.
Hettan gör att kablarnas plastöverdrag smälter och därmed blir segare, vilket leder till större friktion. Detta begränsar den relativa rörelsen vid koppling av kablar och slangar. Ytterligare transportutrymme behövdes, dels för att inrymma fler kablar och slangar, dels för att ge de termiska förbindelserna mer utrymme till kompensation.
Komplext system för ovanlig ansökan
Det redan begränsade utrymmet för kabel- och slangtransportörsystemet blev ännu sämre av att utlastningsanordningen är förankrad med stabilisatorer i väggarna. Av den anledningen var det inte möjligt att använda ett roterande system, vilket visat sig fungera i många andra program. Så en trumma installerades på den bärande utlastningsanordningens fjädring; kabel- och slangtransportörerna är avstängda därifrån och leds istället förbi stabilisatorerna i en högerkurva som går över i en vänsterböj. Men i denna design var en bredare transportör med mer utrymme inte ett alternativ. Kabelschlepp föreskrev en lösning genom att sätta en andra stålbärare högst upp.
Portalen drivs nu med en 15,25 meter lång stålbärare av typen S 2500 i en 4-bandsdesign med en böjningsradie på 2,360 mm och en tomvikt på 1,375 kg. Ovanpå detta en mindre, 14,58 meter lång bärare av typen 1800, också i en 4-bandsdesign med böjningsradie samt omvänd böjningsradie på 1,750 mm och en tomvikt på 732 kg. På så sätt glider de två ståltransportörerna exakt på varandra, banden försågs med manualplattor. De två transportörerna spelade i förhållande till varandra, både i rörelse och i vila. Med denna lösning garanteras även ersättning för kablar och slangar.
Eftersom transportörsystemet bär olika typer av kablar och slangar med lika storlekar, blev det uppenbart att med ramintervaller på 500 mm skulle de jämförelsevis tunna signalkablarna pressas ut under rörelse; de har otillräcklig böjningsstyvhet jämfört med elkablar och slangar med tjockled på upp till 83 mm. Men på grund av design som multipel-bandtransportören och den nödvändiga transportörens storlek hade, kunde stoppintervaller inte göras med en mindre pitch.
- Stagen måste alltid vara utrustade med en förskjutning på en länk, det är inte möjligt att skapa en direkt anslutning mellan olika stopp, säger Wienbeck. Vi har alltid behövt två platser för utrymmet av ramens olika stopp. För 2500S med en 250 mm delningdimension finns ett mellanrum på 500 mm, vilket är oundvikligt.
Små styrkablar med diameter 10 mm är för mycket, de skulle bågna och förstöras. För att ge ytterligare stabiliserande stöd var kablar med låg böjstyvhet och små diametrar dragna i plastbärare av Mono- och Uniflex-serien, dessa i sin tur monterades i den stora ståltransportören – alltså för att permanent förhindra svikt i de mindre kablarna. Fördelarna med aluminiumvistelser var tydliga: 1 – de ger den nödvändiga stabiliteten, 2 – aluminium är en perfekt friktionspartner för kablar och slangar som vilar på materialet. Tack vare de gynnsamma ytegenskaperna är det möjligt att avsesvärt minska friktionen mot kabelbeklädnaden och även från jacketslitage. Detta är särskilt viktigt när man betänker att strömkablarna även kyls med vatten. Skador på isoleringen kan i vissa fall leda till ett totalt misslyckande med avbrytning av tumörbehandling som följd. Med tanke på den stora mängd värme som genereras inom systemet, är aluminium även positivt för dess värmeledande egenskaper. Aluminium absorberar värmen från kablarna och slangarna och släpper ut hettan i luften via ståltransportörer. Kombinationen av material i kabel- och slangsystemen ger därmed en svalkande effekt och skyddar mot överhettning.
- Program som detta visar att det är viktigt att ha olika material i en produktportfölj. Detta innebär att du har lösningar för alla eventualiteter och kan erbjuda en objektiv rådgivning, och du kan täcka alla användningsområden, säger Wienbeck och betonar vikten av Kabelschlepps sortiment med kabel- och slangtransportörer av stål-, plast- och hybrid-design.
Förutom de enorma krafter som kabel- och slangtransportörssystemet utsätts för, är stålbärare det enda möjliga valet på grund av hög mekanisk belastning. Plast ändrar sin struktur under sådana förhållanden, vilket förkortar livslängden av materialet och därmed även livslängden på utlastningsanordningen. Underhåll av systemet innebär väntetid för cancerpatienterna.
Modern teknologi har förändrat nästa alla aspekter av livet till mer bekväma – i många fall är det mycket viktigt. Detta gäller särskilt inom området för medicinsk teknik. Ambitiös forskning och utveckling pågår inom många områden i förhoppning om att finna innovativa lösningar till problem. Detta har nu resulterat i ett system för behandling av tumörer hos cancerpatienter: Heidelberg Ion Beam Therapy Center (HIT) vid Heidelberg Universitetssjukhus är ett delvis underjordiskt högteknologiskt center på tre våningar, i storlek ungefär som en fotbollsplan, där tunga joner accelereras till tre fjärdedelar av ljusets hastighet och sedan styrs exakt in i tumören. Tunga joner skiljer sig avsevärt från vanlig röntgen eller gammastrålning, efterson de verkar på djupet. Tack vare state-of-the-art-teknologi kan de riktas med stor precision, vilket ger mindre skador på omgivande frisk vävnad.
HIT har ett antal egenskaper som gör det världsunikt. En av dem är utlastningsanordningen, en vägledande roterande stråle för tunga joner, i motsats till de två horisontella stationerna för strålbehandling, där jonstrålen släpps ut från ett sugrör i väggen och börjar verka på patienten som är placerad framför den. I det tredje behandlingsrummet styrs balken mot patienten från olika håll för att uppnå den optimala behandlingsvinkeln. Med extrem precision avviker balken från målet med högst en halv millimeter.
Bryter ny teknisk mark
Detta är möjligt genom den omfattande utlastningsanordningskonstruktionen bakom kulisserna. Den rörliga balken av överföringssystem med vakuumrör är upphängd i en komplex ram som liknar de som används för radioteleskop. Denna koloss är tre våningar hög med en total vikt på 670 ton, varav 600 är lösa. Utveckling, leverans, montage och drifttagning av utlastningsanordningen vilar på MT Mechatronics GnbH i Marinz, i samarbete med Centre for Heavy Ion Reserach, Darmstadt. MT Mechatronics är en del av MT Aerospace AG i Augsburg, en etablerad leverantör till flyg- och försvarsindustrin och en erfaren systempartner för antenner, teleskop och mekatroniska system.
Första uppdraget för MT Mechatronic var att genomföra en studie för undersökning av de fysiska förutsättningarna att använda en lämplig struktur till att styra jonstrålen, som är paketerad och överförd i magneter som väger ton, samtidigt som hänsyn tas till effekterna av fysiska krafter och temperaturförhållanden. Byggnaden uppfördes enligt de ursprungliga planerna, men under projektets genomförande stod det klart att det fanns ett mycket begränsat utrymme för utlastningsanordningen. Även om detta problem skulle kunna åtgärdas med hjälp av ett fåtal konstruktionsändringar, fanns fortfarande ett stort hinder som måste övervinnas: kabel- och slangtransportörer som hjälper till att få liv i kolossen så att den kan användas för tumörbehandlingar. Redan detta var en utmaning, med tanke på de mycket komplicerade förhållandena, men det hela skulle ju också utformas extremt kompakt.
- Även för mindre krävande applikationer är få kablar och slangar rätt ofta ett stort problem för transportören. Lösningen baseras främst på användarens specifikationer, säger ingenjör Martin Süß från System Engineering på MT Mechatronics.
Gällande portalkranar var den huvudsakliga inriktningen på de typiska kraven att peka på riktigheten i balkens vägledning och justeringens hastighet.
- Vi var hela tiden uppmärksamma på dessa punkter under projektets gång. Och till sist blev slutsatsen: vi kommer att behöva lägga ytterligare en kabel där.
Süß vet detta av erfarenhet. Och eftersom erfarenheten visar att det inte är så enkelt att ordna behövdes en partner på samma nivå. Det är därför MT Mechatronic, specialist på prototyper av byggnadskonstruktioner och pilotprojekt, litar på erfarenhet och know-how av en annan specialist. Som uppfinnare av kabel- och slangbärare, och som företag med ett brett spektrum av produkter, har Kabelschlepp inte enbart rätt komponenter för att tillhandahålla skräddarsydda lösningar, utan framför allt decennier av praktisk erfarenhet med bred variation av applikationer och miljövillkor. Ingenjör Klaus Scheidel från Project Management hos MT Mechatronic, och den som ansvarar för byggandet av utlastningsanordningen, vet även detta:
- För oss är erfarenhet den avgörande faktorn, liksom flexibilitet och kreativa idéer. Leverantörer med dessa egenskaper identifierar sig med problemen och är fast beslutna att hitta en lösning, även när det blir komplicerat. Och Kabelschlepp har klarat detta test med utlastningsanordningen.
Masterförändringar planeras
Andreas Wienbeck, från kabel- och slangtransportsystemets projektplanering i Siegen, gav sitt stöd till utlastningsanordningsprojektet. Från hans mångåriga erfarenhet vet han följande:
- Den ursprungliga situationen är alltid densamma: du tar ett definierat antal kablar och slangar som måste läggas samt vissa villkor för tillämpningen. Dessa används i planerigen. Med finns alltid ett stort antal förändringar och andra saker som måste bearbetas innan allt fungerar rätt.
Det var samma sak med utlastningsanordningen. Till de kablar och slangar som ursprungligen var planerade anslöt sig ett stort antal nya. Till sist skulle en kabel och en slang som väger 150 kg /m, och upp till 15000 Nm, täckas vilket innebar att valet av material för transportörsystemet skedde mer eller mindre automatiskt.
- Det är inget tvivel om att stål är vårt val av material, säger Wienbeck. Stålets bärare är också strålningsresistenta på lång sikt, också det en viktig faktor när det handlar om driften av portalkranar.
På ett tidigt stadium stod det klart att på grund av det kraftigt ökade antalet kablar och slangar skulle det planerade transportörutrymmet inte vara tillräckligt. Dessutom var strålningsvärmen på kablarnas ytterhölje i vissa fall över 70°C, de som ger stöd till 130 metriska ton magnetbalkarna. På grund av den värme som alstras var kompensationen för kabel- och slangdragning inte längre möjlig – det var en fara med att sätta fast dem.
- Strömförsörjningskablar till magneter bär en enormt stark ström. För att skydda systemet mot överhettning kyls kablarna med vatten i kylslangar. Tyvärr visade det sig att värmeutvecklingen ändå var ganska hög, säger experten från Kabelschlepp.
Hettan gör att kablarnas plastöverdrag smälter och därmed blir segare, vilket leder till större friktion. Detta begränsar den relativa rörelsen vid koppling av kablar och slangar. Ytterligare transportutrymme behövdes, dels för att inrymma fler kablar och slangar, dels för att ge de termiska förbindelserna mer utrymme till kompensation.
Komplext system för ovanlig ansökan
Det redan begränsade utrymmet för kabel- och slangtransportörsystemet blev ännu sämre av att utlastningsanordningen är förankrad med stabilisatorer i väggarna. Av den anledningen var det inte möjligt att använda ett roterande system, vilket visat sig fungera i många andra program. Så en trumma installerades på den bärande utlastningsanordningens fjädring; kabel- och slangtransportörerna är avstängda därifrån och leds istället förbi stabilisatorerna i en högerkurva som går över i en vänsterböj. Men i denna design var en bredare transportör med mer utrymme inte ett alternativ. Kabelschlepp föreskrev en lösning genom att sätta en andra stålbärare högst upp.
Portalen drivs nu med en 15,25 meter lång stålbärare av typen S 2500 i en 4-bandsdesign med en böjningsradie på 2,360 mm och en tomvikt på 1,375 kg. Ovanpå detta en mindre, 14,58 meter lång bärare av typen 1800, också i en 4-bandsdesign med böjningsradie samt omvänd böjningsradie på 1,750 mm och en tomvikt på 732 kg. På så sätt glider de två ståltransportörerna exakt på varandra, banden försågs med manualplattor. De två transportörerna spelade i förhållande till varandra, både i rörelse och i vila. Med denna lösning garanteras även ersättning för kablar och slangar.
Eftersom transportörsystemet bär olika typer av kablar och slangar med lika storlekar, blev det uppenbart att med ramintervaller på 500 mm skulle de jämförelsevis tunna signalkablarna pressas ut under rörelse; de har otillräcklig böjningsstyvhet jämfört med elkablar och slangar med tjockled på upp till 83 mm. Men på grund av design som multipel-bandtransportören och den nödvändiga transportörens storlek hade, kunde stoppintervaller inte göras med en mindre pitch.
- Stagen måste alltid vara utrustade med en förskjutning på en länk, det är inte möjligt att skapa en direkt anslutning mellan olika stopp, säger Wienbeck. Vi har alltid behövt två platser för utrymmet av ramens olika stopp. För 2500S med en 250 mm delningdimension finns ett mellanrum på 500 mm, vilket är oundvikligt.
Små styrkablar med diameter 10 mm är för mycket, de skulle bågna och förstöras. För att ge ytterligare stabiliserande stöd var kablar med låg böjstyvhet och små diametrar dragna i plastbärare av Mono- och Uniflex-serien, dessa i sin tur monterades i den stora ståltransportören – alltså för att permanent förhindra svikt i de mindre kablarna. Fördelarna med aluminiumvistelser var tydliga: 1 – de ger den nödvändiga stabiliteten, 2 – aluminium är en perfekt friktionspartner för kablar och slangar som vilar på materialet. Tack vare de gynnsamma ytegenskaperna är det möjligt att avsesvärt minska friktionen mot kabelbeklädnaden och även från jacketslitage. Detta är särskilt viktigt när man betänker att strömkablarna även kyls med vatten. Skador på isoleringen kan i vissa fall leda till ett totalt misslyckande med avbrytning av tumörbehandling som följd. Med tanke på den stora mängd värme som genereras inom systemet, är aluminium även positivt för dess värmeledande egenskaper. Aluminium absorberar värmen från kablarna och slangarna och släpper ut hettan i luften via ståltransportörer. Kombinationen av material i kabel- och slangsystemen ger därmed en svalkande effekt och skyddar mot överhettning.
- Program som detta visar att det är viktigt att ha olika material i en produktportfölj. Detta innebär att du har lösningar för alla eventualiteter och kan erbjuda en objektiv rådgivning, och du kan täcka alla användningsområden, säger Wienbeck och betonar vikten av Kabelschlepps sortiment med kabel- och slangtransportörer av stål-, plast- och hybrid-design.
Förutom de enorma krafter som kabel- och slangtransportörssystemet utsätts för, är stålbärare det enda möjliga valet på grund av hög mekanisk belastning. Plast ändrar sin struktur under sådana förhållanden, vilket förkortar livslängden av materialet och därmed även livslängden på utlastningsanordningen. Underhåll av systemet innebär väntetid för cancerpatienterna.